- News & Insights
- 2024
- How to Overcome Logistical Challenges in Healthcare Equipment Deliveries and Installations
- Healthcare Equipment
- Industries
How to Overcome Logistical Challenges in Healthcare Equipment Deliveries and Installations
Handling heavy, bulky, and expensive medical equipment, such as MRI, CT, and PET scanners, requires meticulous planning and coordination.
The medical device market is booming, driven by the rising demand for cutting-edge healthcare solutions. As chronic diseases become more widespread, so does the need for innovative devices to improve patient care. However, while creating such devices is undoubtedly complex, ensuring their safe and timely delivery poses an even greater challenge—especially in the case of large, fragile equipment.
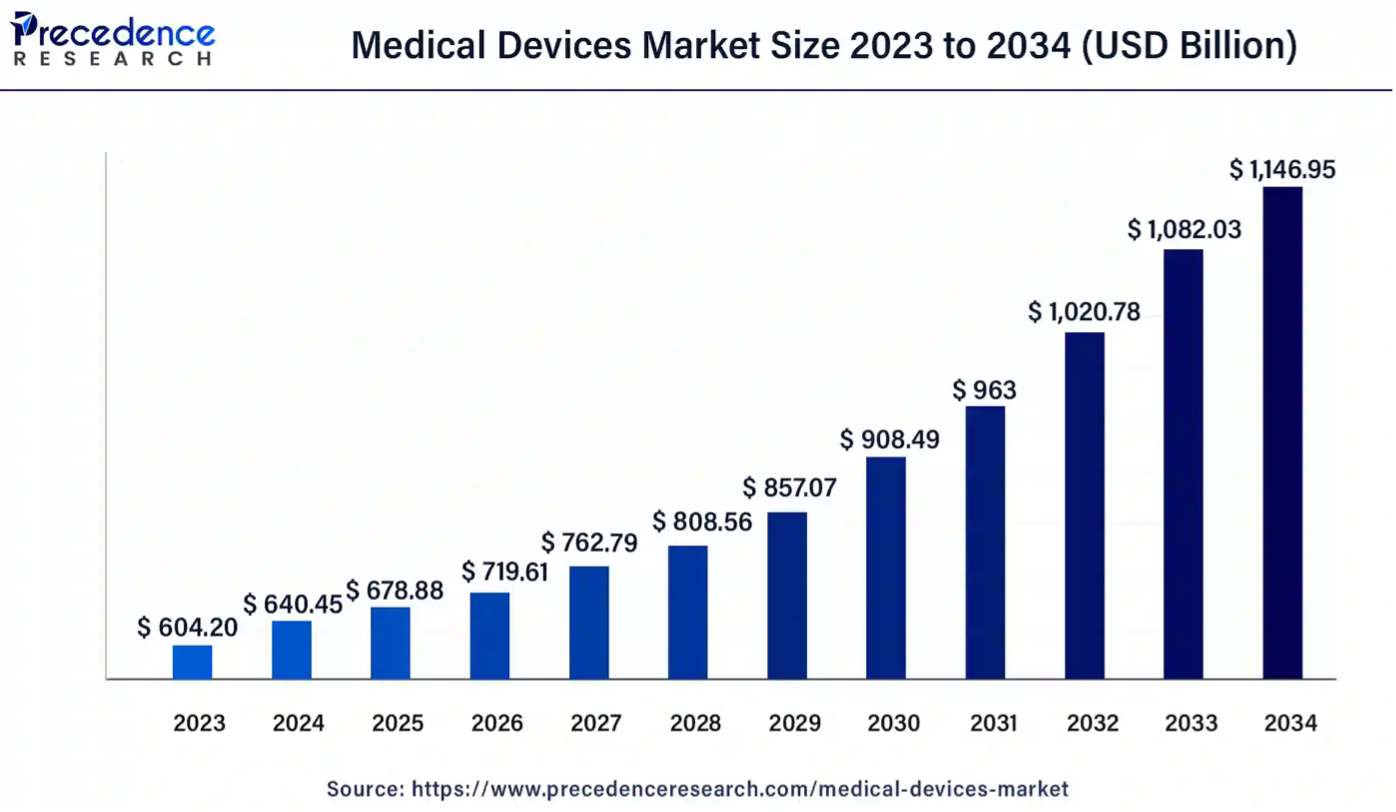
Rising investments in Research & Development (R&D) by medical technology companies, coupled with streamlined regulatory approvals for advanced devices, are expected to drive market growth in medical devices in the coming years. Source: Precedence Research
The Challenges of Transporting Heavy Healthcare Equipment
Handling heavy, bulky, and expensive medical equipment, such as MRI, CT, and PET scanners, requires meticulous planning and coordination. These machines, which can weigh up to 17 tons 1, present significant logistical challenges due to their size and sensitivity to vibrations, shocks, and the external environment. For example, moving an MRI machine is a very complex task that demands protective packaging designed to withstand transportation stress while ensuring the machine's safety and functionality. MRI machines are costly, with their prices varying based on factors like magnet strength, brand, and model.2 According to Money Magazine, the total cost of purchasing and installing an MRI machine ranges from $3 million to $5 million 3. Adding to the challenge, MRIs rely on liquid helium to maintain supercooled temperatures, and any disruption can cause a "quench," rendering the machine inoperable4. Therefore, MRIs must be transported in a temperature-controlled environment.
Addressing Installation Delays
In any industry, delays in installation due to missing or damaged parts are common, affecting 20-40% of projects5. In healthcare, such delays can have serious consequences, potentially disrupting life-saving scans and treatments. The installation of medical imaging equipment machines is susceptible due to the equipment's complexity and the critical role it plays in diagnostics. A missing component or a malfunction during setup could delay patient care, leading to longer wait times or even postponed procedures. Proper planning and execution are critical to avoiding damage and ensuring successful installation. Fortunately, specialized installation management solutions can help minimize these risks, ensuring that imaging equipment machines are delivered and installed on time and without issue.
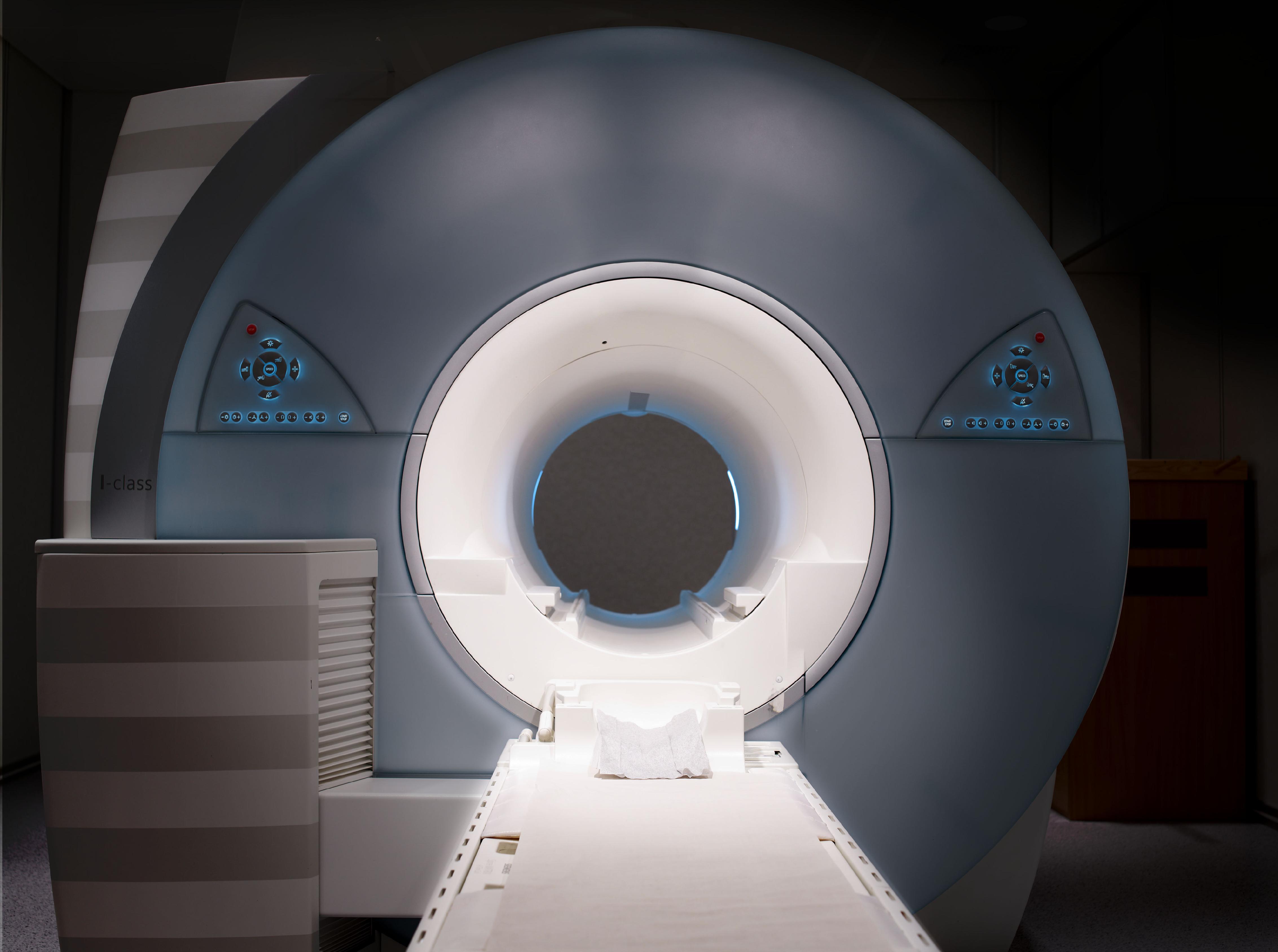
Medical imaging equipment is crucial for accurate disease diagnosis, but it can be expensive and subject to installation delays if the logistic process is not managed effectively.
What are Installation Management Services (IMS)?
Nefab’s Installation Management Solution (IMS) provides a more flexible alternative to its Last Mile Optimization programs, offering tailored options to fit specific needs and budgets. Ideal for complex installations involving multiple accessory crates, intricate supply chains, and shipments from various origins, IMS ensures smoother operations by incorporating advanced logistics planning, real-time tracking, and proactive coordination. This approach addresses critical details, such as monitoring temperature-sensitive components like helium and minimizing risks such as equipment damage during transit. By streamlining the entire process, IMS helps ensure the integrity of the equipment while optimizing the overall installation timeline.
Two-Phase Approach
To ensure maximum efficiency and precision in the complex logistics process, Nefab implemented a strategic two-phase approach that addresses both planning and real-time execution.
- Phase 1 focuses on meticulous planning, modeling, and connectivity, covering everything from packaging requirements to loading instructions. This phase integrates seamlessly with a comprehensive tracking platform, providing visibility and coordination across the entire supply chain.
- Phase 2 kicks in with real-time monitoring and shipment management, allowing for immediate corrective actions whenever necessary to keep timelines on track.
This two-phase approach dramatically reduces the risks of missing or damaged parts, minimizes man-days on-site, and streamlines the integration of devices from various vendors. The result? "First-time-right" installations that enhance operational efficiency and customer satisfaction. What does this look like in practice? A smooth, streamlined process where projects are delivered on time with fewer disruptions and greater precision.
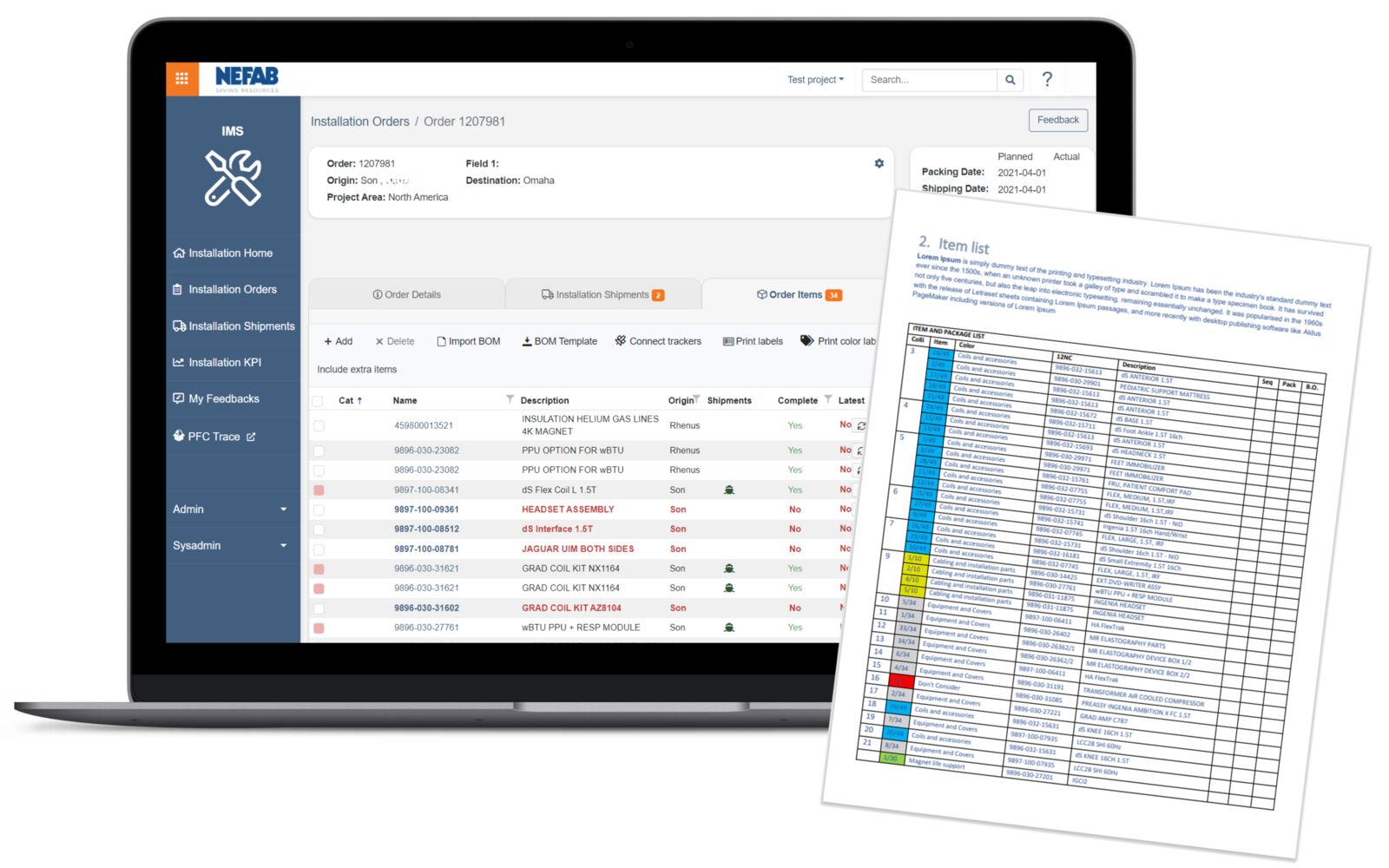
Installation Management Platform allows to plan, track, and manage your installation process in real-time, ensuring parts arrive on time and undamaged, while identifying potential issues before they cause delays.
Coordinated Delivery In Practice
A leading medical imaging manufacturer faced significant challenges in shipping MRI machines, which required multiple components to be sent in separate boxes across different locations. The shipments were tested at five global sites—Germany, the US, the UK, China, and Japan—each with its own unique obstacles, from hard-to-access areas to large warehouses with varying levels of accessibility and storage conditions. Poor delivery coordination led to costly delays, often caused by missing, damaged, or incorrect parts, especially as third-party installers were hired to set up the equipment. To address these problems, Nefab partnered with the manufacturer to streamline deliveries and installations. The company introduced protective overpacks to prevent damage, implemented tracking systems to quickly identify and resolve issues, and used planning kits to minimize packing and loading errors. Nefab also introduced color-coding of items to speed up and simplify the installation process. This two-year project not only saved the company over €900K (USD 1M) annually but also earned Nefab the prestigious "Supplier Excellence Award" in 2020.
Optimizing Healthcare Equipment Installations
The complexities of transporting and installing heavy medical equipment demand precision and coordination that only advanced logistics solutions can provide. Nefab’s Installation Management Solution (IMS) addresses these challenges with its flexible, two-phase approach, ensuring efficient, on-time installations and minimizing potential delays or equipment damage. By offering tailored solutions, real-time monitoring, and improved logistical planning, IMS enhances operational efficiency and delivers substantial cost savings, as demonstrated by the successful pilot program. With IMS, healthcare providers can ensure that their critical equipment arrives safely and is installed smoothly, improving patient care and satisfaction.
We save resources in supply chains for a better tomorrow.
Want to learn more?
GET IN TOUCH
Contact us to learn more about our smart and sustainable solutions.
LEARN MORE
Solutions for the Healthcare industry
Optimize Your Supply Chain with Sustainable, Regulatory-Compliant Solutions
GreenCalc
Nefab’s own certified calculator measures and quantifies financial and environmental savings in our solutions